ZERON 100 (SUPERNOVA 100) Slickline
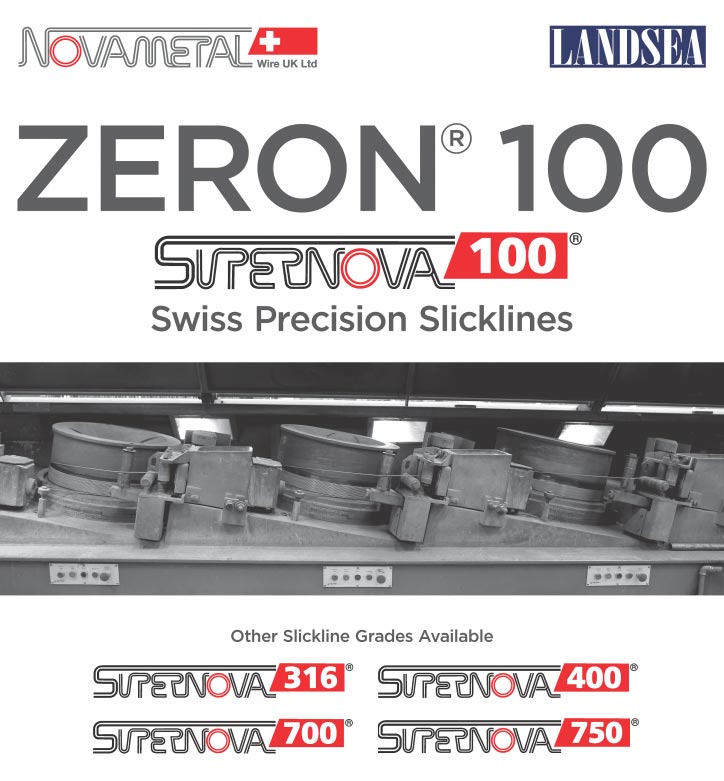
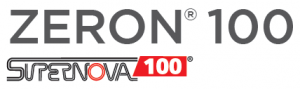




Contact Us For More Information
sales1@isea.com.sg
www.novametal.co.uk
Supernova 100 ®, 316 ®, 400 ®, 700 ®, And 750 ® are the registered trademarks of Novametals SA Zeron® is a registered trademark of rolled Alloys
UNS S32760 WN 1.4501 PRE: >41
In addition to excellent mechanical properties, ZERON® 100 (Supernova 100®) slicklines have exceptional resistance to chloride and sulphide stress corrosion cracking, acid corrosion and crevice corrosion making it suitable for a wide range of corrosive sour well environments.
Manufactured in Switzerland and certified to 9001: 2008 all Supernova Slicklines are fully traceable, 100% Weld Free, 100% Eddy Current Tested and Wrap Tested.
Being the sole exclusive manufacturer of Zeron 100 Slicklines, we are committed to our customers in producing the best qualitied Zeron 100 Slicklines in our Switzerland mill.
All are produced with a consistent, tightly controlled surface finish, wire helix and wire cast for optimal spooling and in-service performance.
ZERON 100 (SUPERNOVA 100) Slickline
In addition to excellent mechanical properties, ZERON® 100 (Supernova 100®) slicklines have exceptional resistance to chloride and sulphide stress corrosion cracking, acid corrosion and crevice corrosion making it suitable for a wide range of corrosive sour well environments.
Manufactured in Switzerland and certified to 9001: 2008 all Supernova Slicklines are fully traceable, 100% Weld Free, 100% Eddy Current Tested and Wrap Tested.
Being the sole exclusive manufacturer of Zeron 100 Slicklines, we are committed to our customers in producing the best qualitied Zeron 100 Slicklines in our Switzerland mill.
All are produced with a consistent, tightly controlled surface finish, wire helix and wire cast for optimal spooling and in-service performance.
Key Characteristics
- Outstanding resistance to chloride-induced stress corrosion cracking (SCC) and sulphide-stress cracking (SSC) in sour-gas conditions
- Resistant to SSC in sour, condensed waters with 0.4 bar partial pressure of H2S
- Outstanding corrosion resistance under warm seawater conditions, along with superior pitting resistance
- High break loads with good ductility
- May be used in temperatures up to 300°C
- Good atmospheric corrosion enabling safe marine / offshore storage
- High resistance to abrasion, fatigue and corrosion fatigue
- Very resistant in sweet wells, to corrosion by CO2
Key Characteristics
- Outstanding resistance to chloride-induced stress corrosion cracking (SCC) and sulphide-stress cracking (SSC) in sour-gas conditions
- Resistant to SSC in sour, condensed waters with 0.4 bar partial pressure of H2S
- Outstanding corrosion resistance under warm seawater conditions, along with superior pitting resistance
- High break loads with good ductility
- May be used in temperatures up to 300°C
- Good atmospheric corrosion enabling safe marine / offshore storage
- High resistance to abrasion, fatigue and corrosion fatigue
- Very resistant in sweet wells, to corrosion by CO2
Key Data
Standard Diameter (Inches) | Minimum Breaking Load* (lbf) | Min Tensile (N/mm2) (Ksi) | Nominal Weight (lbs/ 1000ft) | Minimum Sheave Diameter (Inches) | |
0.092 | 1750 – 1800 | 1805 | 263 | 22.10 | 11 |
0.108 | 2350 – 2400 | 1800 | 260 | 30.55 | 13 |
0.125 | 3150 – 3200 | 1820 | 261 | 41.03 | 15 |
0.140 | 3950 – 4050 | 1760 | 263 | 51.54 | 17 |
0.160 | 5050 – 5150 | 1760 | 256 | 67.45 | 20 |
Tolerance +/-0.001″ – other diameters are available on request.
* When using a portable wire tester expect a MBL figure up to 25% less than the true figure obtained on our in-house calibrated equipment.
Chemical Composition
Element | C | Si | Mn | P | S | Cr | Mo | Cu | Ni | N | W | |
Weight % | Min | – | – | – | – | – | 24.50 | 3.00 | 0.50 | 6.00 | 0.20 | 0.50 |
Max | 0.03 | 1.00 | 1.00 | 0.03 | 0.015 | 26.00 | 4.00 | 1.00 | 8.00 | 0.30 | 1.00 |
Corrosion Resistance PRE Number (PRE)
PRE: >41
PRE = Cr + 3.3 x Mo + 16 x N
Pitting Resistance Equivalent numbers (PRE) are a way of comparing the pitting corrosion resistance of
various stainless steels based on the levels of chromium, molybdenum and nitrogen they contain with the most frequently used formula and Novametal’s preferred method for calculating PRE numbers being :
PRE = Chromium + 3.3 x Molybdenum + 16 x Nitrogen.
Some suppliers may use a factor of 30 x N, resulting in a marginally inflated PRE Number.
Other Slickline Grades
To request for a detailed specification of these wireline (slicklines), please